Solar energy is really starting to get its wings, with utility and residential installation growing at a rapid clip. While these systems generally operate for two or three decades, there inevitably comes a time to take photovoltaic panels down for replacement. What happens then has a lot to say about solar's long-term bottom line.
The opportunity is there to turn old PV panels into new ones, reducing the technology's environmental footprint. But in a paper published in Nature Sustainability, a group led by Garvin Heath at the US National Renewable Energy Laboratory argues we have a long way to go—though they think they see the way.
A matter of purity
Currently, they say, standard practice is to hand solar panels to existing glass- or metal-recycling facilities—at best, batches of panels may be at least be run through on their own. That does little more than recover the aluminum in the frame, the copper in the wiring, and the glass sheet atop the photovoltaic cells. Laws mandating panel recycling haven't advanced beyond the drawing board in many places yet, with the European Union and the state of Washington in the US as exceptions. The EU requires at least 75 percent of material to be recovered, and these processes can hit that mark.
Only Europe has recyclers focused purely on panels. The relatively small number of panels currently being disposed of, along with the limited value of recovered materials, means many don't yet see opportunity. In the United States, the authors write, "Based on anecdotal reports, some modules are being disposed in municipal (non-hazardous) and hazardous landfills. Others are being stored until lower-cost and easier recycling options develop, accumulated quantities become more economical to ship and recycle, and issues such as testing for hazardous waste determination (toxic contaminant leach testing)—which affect interstate transport and treatment options and costs—are resolved."
Recycle everything
Dedicated recyclers are needed, the authors write, to do a more thorough job of recycling all the components of a panel—including the crystalline silicon in the photovoltaic cells themselves. Silicon wafers account for about half the cost of a panel, as well as over half the energy and carbon footprint of manufacturing a panel. But silicon isn't currently being targeted for recycling much because the recovered silicon isn't pure enough to go straight back to a wafer manufacturer. The "metallurgical-grade" silicon that comes from recycling nets about $2 per kilogram on the market, while purer silicon would fetch $10 per kilogram. That would totally change the equation for recyclers.
The techniques for getting to higher purities aren't a total mystery—after all, silicon is being purified from mined quartzite currently. But those processes have been tuned to the exact characteristics and impurities of the raw materials. Recycling wafers would mean tuning the purifying process to a new material, accounting for the variety of other elements present in photovoltaic cells. The authors say one thing holding back recyclers is actually a lack of available data on the impurities in solar cells, making it difficult to design a process around them.
Process is key
But it's not just that. The authors point out that many laboratory studies have identified potential methods for specific aspects of the recycling process, but a recycler will need a complete suite of linked methods that can work as part of a single process. That's where engineering comes in—finding ways to integrate things into a process.
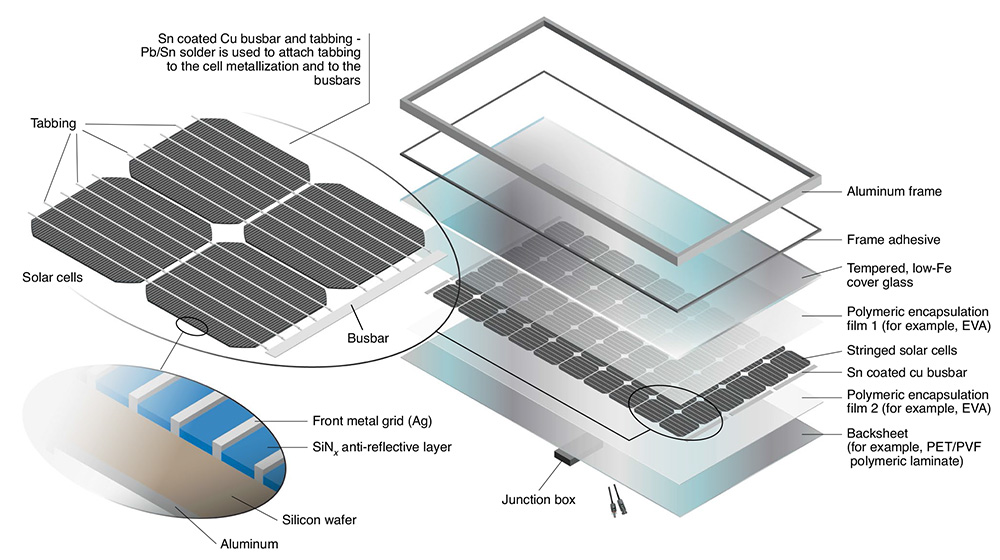

arstechnica
[contfnewc] [contfnewc]