Velodyne invented modern three-dimensional lidar scanners in the mid-2000s. But in recent years, the conventional wisdom has held that Velodyne's design—which involved mounting 64 lasers onto a rotating gimbal—would soon be rendered obsolete by a new generation of solid-state lidar sensors that used a single stationary laser to scan a scene.
But a startup called Ouster is seeking to challenge that view, selling Velodyne-like spinning lidar sensors at competitive prices. In late April, we talked to Ouster CEO Angus Pacala, who has special expertise on the tradeoffs between spinning and solid-state lidars. The reason: Pacala was previously a co-founder at Quanergy, one of the best-known startups working on solid-state lidar.
In our conversation, Pacala declined to badmouth his former company. But actions speak louder than words here. We can assume that as a Quanergy cofounder, Pacala became intimately familiar with the strengths and weaknesses of solid-state lidar technologies. And so it's telling that when he decided to create another lidar company, he decided not to do another solid-state one.
"Solid state lidar" is actually an umbrella term that covers several non-spinning lidar designs. There's an approach called MEMS—microelectromechanical systems—that involves using a tiny mirror to steer a laser beam. Other solid state lidars use a technology called optical phased arrays to steer a laser beam with no moving parts. A third category, called flash lidar, dispenses with beam steering and simply illuminates the entire scene in a single flash, detecting the returned light with a two-dimensional array of sensors akin to a digital camera.
Pacala's old company, Quanergy, hasn't explained its technology in any detail. But it has reportedly focused on the phased-array approach.
With little or no moving parts, all three of these designs have the potential to be cheap and rugged. In the long run, advocates envision packing almost all of the electronics—including the laser itself, beam-steering circuitry, the detector, and supporting computing power—onto a single chip. Solid-state lidars are likely to be less obtrusive in consumer products than bulky spinning lidar that has to stick up from the roof of the car to work well.
This all sounds good in theory, and Pacala presumably thought it was correct when he co-founded Quanergy in 2012. But he has evidently changed his mind, since his second lidar startup uses a more conventional spinning-laser approach.
Spinning lidar has some unique advantages
One of Google's early self-driving car prototypes. Note the giant roof-mounted lidar sensor, the black radar box on the front fender (one of four), and the "wheel encoder" mounted on the back wheel. There were also video cameras inside the cabin. This model had $150,000 worth of extra equipment.[/ars_img]In his conversation with Ars, Pacala pointed out a couple of big advantages of the classic spinning design. The most obvious one is the 360° field of view. You can stick one lidar unit on the top of a car and get a complete view of a car's surroundings. Solid state lidars, in contrast, are fixed in place and typically have a field of view of 120° or less. Hence, it takes at least four units to achieve comparable coverage with a solid-state sensor.
Another less obvious advantage, Pacala says, is that eye safety rules allow a moving laser source to emit at a higher power level than a stationary one.
"All class 1 systems must be designed such that if a person were to put their eyes right up to the device without blinking for many seconds, that they still wouldn't be hurt," he told Ars.
With a scanning solid-state unit, putting your eye inches from the laser scanner could cause 100 percent of the laser light to flood into the eye. But with a spinning sensor, the laser is only focused in any particular direction for a fraction of its 360° rotation. A spinning lidar unit can therefore put more power into each laser pulse without creating risk of eye damage. That makes it easier to detect return flashes, so spinning units may have a range advantage over stationary ones for the foreseeable future.
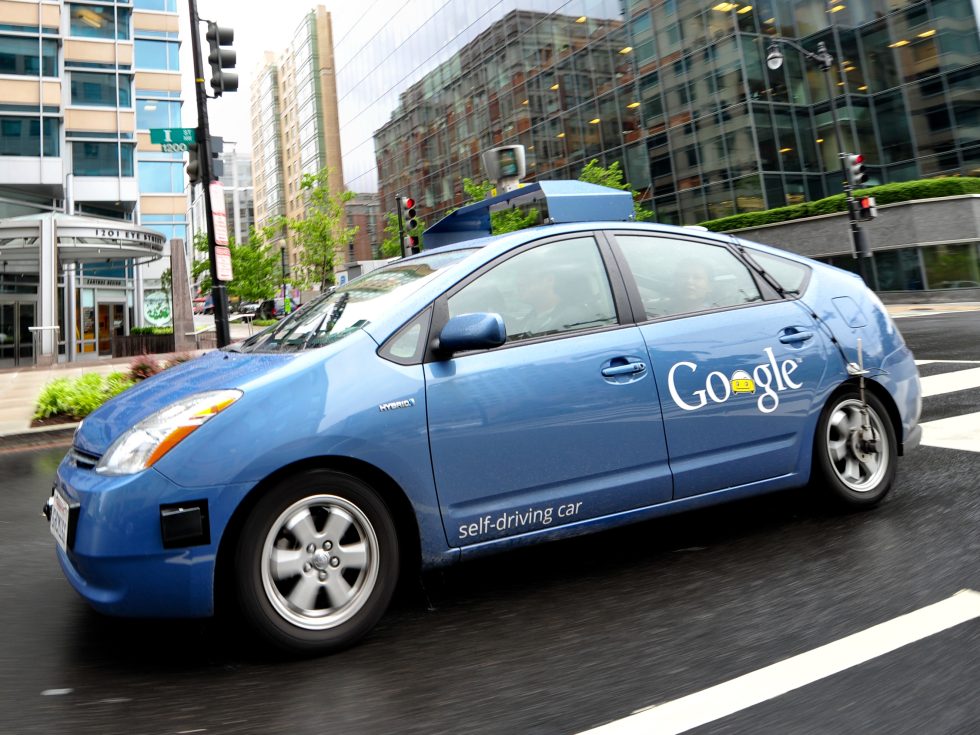
At the same time, most of the leading solid-state designs face significant challenges achieving long range.
- The tiny mirrors in MEMS systems can only reflect so much light. That makes it inherently difficult to bounce a laser beam off a distant object and detect the return flash.
- The phased-array approach tends to produce beams that diverge more than other techniques, making it hard to achieve a combination of long range, high scanning resolution, and wide field of view.
- With flash lidar, the light from each flash is spread over the entire field of view, which means that only a fraction of the light strikes any particular point. And each pixel in the photodetector array is necessarily quite small, limiting the amount of returned light it can capture.
"Solid-state approaches are very challenging," Pacala told Ars. He argues that conventional spinning-lidar techniques have unique strengths that will continue to make them relevant for at least another decade—especially at the high end of the market.
"The vast majority of lidar systems will be solid state" in 10 years, Pacala predicts. "But there's probably still going to be some spinning lidar sensors that are really high performance and a great value."
Pacala drew an intriguing analogy to the hard drive market. Over the last 15 years or so, solid-state storage devices have become increasingly popular, especially in mobile devices. Yet there are still plenty of conventional hard drives with spinning magnetic platters being sold today. That design offers an unbeatable combination of high capacity and low cost.
By the same token, Pacala envisions a future where low-end lidar units are mostly solid state designs, just as most mobile devices today have on-board solid-state storage. But for the most demanding applications—including self-driving cars—he anticipates a significant market for premium spinning lidars that offer long range, high resolution, and a broad field of view.
Ouster is putting price pressure on Velodyne
While Ouster is using the same basic technology approach as Velodyne, the company is offering transparent and aggressive pricing that could create a headache for the Velodyne.
Ouster offers three models—a low-end 16-laser sensor called the OS-1 for $3,500, a 64-laser version of the OS-1 that costs $12,000, and a longer-range 64-laser unit called the OS-2 that costs $24,000.
How does this compare with Velodyne's offerings? Velodyne sells its 16-laser "puck" lidar for $4,000, which is roughly comparable to Ouster's $3,500 16-laser model.
But in an email conversation, I couldn't pin down Velodyne president Marta Hall on the price of Velodyne's more expensive models. As recently as last December, Forbes was reporting that Velodyne's venerable 64-laser model still cost $75,000, only slightly less than its $85,000 price a decade ago.
When I asked Hall how the Velodyne's HDL-64E lidar compares to the 64-laser OS-1, price-wise, she responded: "Velodyne's HDL-64E was developed ten years ago and since then Velodyne has made many improvements. Please compare Ouster's new Lidar product to Velodyne's new Lidar product, the VLS-128. At volume pricing it is $12,000 or less."
It's true that the VLS-128 has more impressive specs than the Ouster's OS-1. Velodyne's high-end unit has a long range that makes it more comparable to Ouster's OS-2, which costs $24,000. How much does one VLS-128 cost? Hall told Ars that it "hasnt been priced yet for single sales." Is that $12,000 price available now for volume customers? She didn't respond.
Ultimately, a lidar unit's single-unit price doesn't matter that much. The long-run goal for all of these lidar companies is to sell sensors in units of thousands or even millions for use in consumer vehicles. A carmaker buying lidar units in batches of 10,000 will obviously get a big discount from the single-unit price.
But publishing a specific price for immediate delivery, as Ouster does, helps to establish credibility. We're sure Velodyne is going to make every effort to match Ouster's $12,000 price at some point in the future. But aiming to do it in the future isn't the same thing as being able to do it today.
We got a similar response last month when we asked Austin Russell, CEO of the lidar startup Luminar, about pricing. He told us that "for consumer vehicles, this type of stuff does need to get down to low single-digit thousands," and promised that this would be "not an issue" for Luminar. Reading between the lines, it sounds like Luminar's lidars are not priced in the "low single-digit thousands"—and indeed might be a lot more than that today.
Overall, my conversation with Ouster's Pacala made me less bullish about improvements in lidar costs. Prices are falling, as illustrated by Velodyne's 50 percent price cut for its 16-laser unit this year. And if you're willing to settle for a lidar with lower range and resolution, you can find units that cost a few thousand or even a few hundred dollars.
But the best lidar units—and possibly the only ones that are suitable for fully driverless cars—still seem to cost tens of thousands of dollars.
It's worth noting that one other major player in lidar technology is Waymo. The Alphabet subsidiary has been working on self-driving cars for almost a decade now, and they've shifted from using Velodyne units to their own home-grown lidar technology.
The company is still using the same basic spinning-laser approach, but has reportedly figured out how to lower the cost of its lidar units by a factor of 10. It's hard to translate that into a specific price since we don't know what their original cost was, but it's safe to say that Waymo's units cost no more than $8,500—and possibly less.
For companies not called Waymo, this may be a problem that solves itself. There's a natural tendency for complex products to fall in price as they are produced in higher volumes. Today the demand for lidar units is a tiny fraction of what it will be in five to 10 years when companies are rushing to expand their driverless taxi fleets. As lidar production expands, improved manufacturing techniques and economies of scale will inevitably make cheaper lidar possible.
[contf] [contfnew]
Ars Technica
[contfnewc] [contfnewc]